Understanding Lathe Machine Parts: A Comprehensive Guide for Metal Fabricators
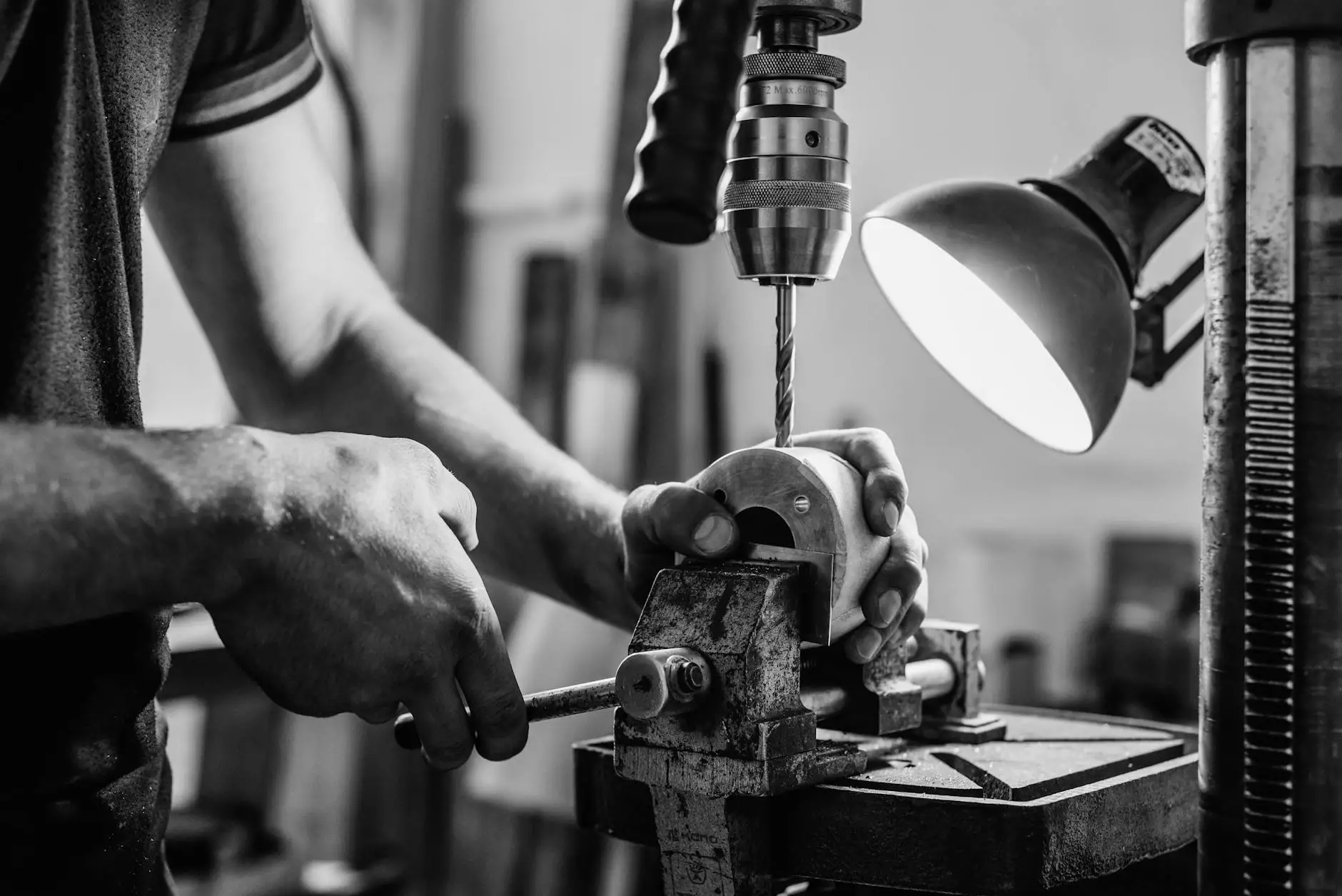
The world of metal fabrication relies heavily on precision engineering and reliable machinery. Among the tools that play a vital role in this field are lathe machines. These machines are not only essential for shaping materials but also for creating intricate components that are crucial in various industries. In this article, we’ll delve deep into the details of lathe machine parts, their functions, and how they are pivotal for metal fabricators.
What is a Lathe Machine?
A lathe machine is a powerful tool used to turn raw material into finished products. Typically, it rotates the workpiece on its axis while a cutting tool is applied to it. This setup allows for the production of various geometrical shapes, including cylinders, spheres, and complex profiles. Understanding the parts of a lathe machine can not only enhance operational efficiency but also improve the quality of the finished products.
Key Components of a Lathe Machine
Lathe machines consist of several important components, each serving a unique purpose in the machining process. Here’s a detailed overview of the most critical lathe machine parts:
1. Headstock
The headstock is one of the primary components of a lathe machine. It houses the motor, gearbox, and other essential mechanisms. The primary function of the headstock is to hold and rotate the workpiece. It usually includes a spindle that can be adjusted for different speeds, allowing for a wide range of machining operations.
2. Tailstock
The tailstock sits opposite the headstock and can be moved along the bed of the lathe. Its main role is to support the other end of the workpiece and can also house tools for drilling operations. Adjusting the tailstock is vital for ensuring accuracy in machining tasks.
3. Bed
The bed is the heavy base of the lathe machine, providing stability and support for the other components. It must be perfectly straight and robust to absorb vibrations during the machining process, ensuring precision and preventing wear and tear over time.
4. Carriage
The carriage moves along the length of the lathe bed and houses the tool post and cutting tools. It is responsible for controlling the position of the cutting tool relative to the workpiece, allowing for intricate operations such as turning, facing, and boring.
5. Tool Post
The tool post is mounted on the carriage and holds the cutting tool in place. Its design allows for quick changes and adjustments, enabling metal fabricators to switch between different operations without significant downtime.
The Importance of Lathe Machine Parts in Metal Fabrication
Understanding the various lathe machine parts is crucial for any metal fabricator. Each component plays a vital role in the machining process, affecting everything from precision to efficiency. Here are some reasons why knowledge of these parts is beneficial:
Enhanced Precision and Quality
When metal fabricators understand the function of each part, they can optimize their machining processes to achieve higher levels of precision. For instance, proper adjustment of the tailstock and tool post can significantly enhance the dimensional accuracy of the components being produced.
Operational Efficiency
Familiarity with lathe machine parts allows fabricators to perform maintenance more effectively. Regular checks and timely replacements of worn-out parts can minimize downtime and ensure the machine operates at peak performance.
Cost Savings
Investing time in understanding and optimizing the use of lathe machine parts can lead to substantial cost savings. Enhanced efficiency leads to less material waste and improves product quality, which can boost the profitability of a metal fabrication business.
Common Lathe Machine Parts and Their Functions
Below is a comprehensive list of common lathe machine parts and their functions:
- Spindle: Holds and rotates the workpiece.
- Chuck: Attaches the workpiece to the spindle.
- Apron: Controls the movement of the carriage.
- Cross Slide: Provides lateral movement of the cutting tool.
- Feed Rod: Drives the carriage for automatic movement.
- Lead Screw: Used for threading operations.
- Power Switch: Powers on and off the machine.
Types of Lathe Machines
Lathe machines come in various types, each designed for specific tasks. Here are some common types:
1. Engine Lathe
The engine lathe is the most common type of lathe, capable of performing a wide range of operations. It offers various speed settings and is versatile for both small and large fabrications.
2. Turret Lathe
The turret lathe is designed for repetitive production and features multiple tool stations. This helps in increasing efficiency for bulk manufacturing of similar components.
3. CNC Lathe
CNC lathes (Computer Numerical Control) are automated machines that work with enhanced precision. They require programming to perform complex cuts and shapes, making them ideal for modern manufacturing needs.
4. Mini Lathe
Mini lathes are compact machines designed for hobbyists or small-scale operations. They provide excellent functionality in a smaller footprint, suitable for intricate works.
Maintaining Lathe Machine Parts
Regular maintenance of lathe machine parts is crucial to ensure longevity and efficiency. Here are some maintenance tips:
1. Regular Lubrication
Lubricating the moving parts helps reduce friction and wear. Ensure that grease and oil are applied as per the manufacturer's guidelines.
2. Cleaning
Keep the lathe machine clean from debris and dust. Cleaning the bed, chuck, and other surfaces reduces the risk of corrosion and promotes precise machining.
3. Calibration
Regularly calibrate the lathe for accuracy. Small deviations can lead to significant errors in the finished product.
Conclusion
Understanding and maintaining lathe machine parts is paramount for metal fabricators aiming for excellence in precision engineering. Each component plays a critical role, impacting the quality, efficiency, and profitability of machining operations. As technology continues to evolve, staying informed about the latest advancements and maintenance strategies can ensure that metal fabricators remain competitive in a dynamic market. For further information, resources, and assistance, explore our offerings at DeepMould.net.